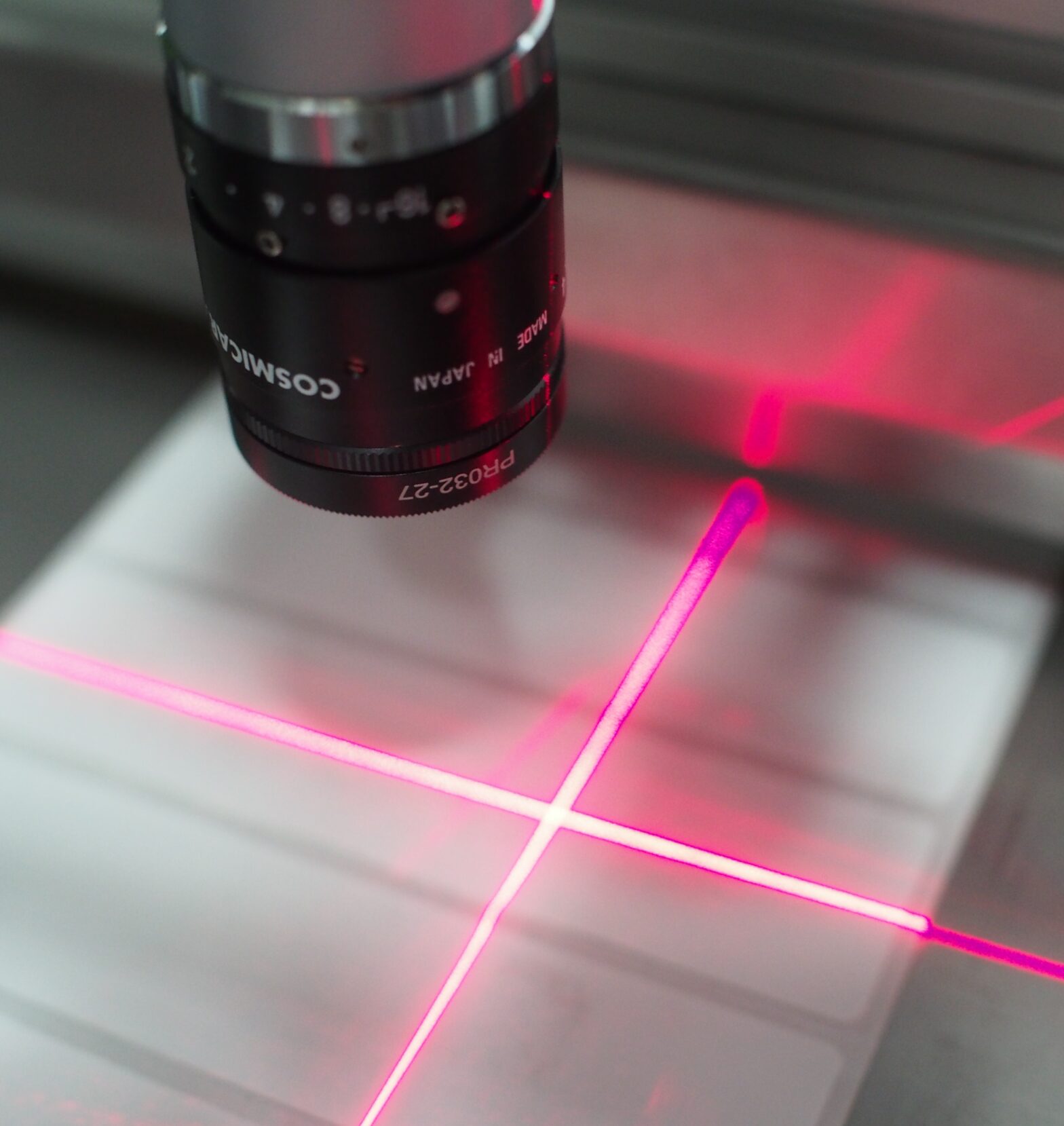
AUTOMATISERET KVALITETS KONTROL SYSTEMER
Visionssystemer til kvalitetskontrol anvendes i produktions- og lagerområder. De muliggør automatiseret inspektion af produkter, der bevæger sig på produktionslinjerne. De verificerer varernes overensstemmelse med specifikationen, korrektheden af montering, emballering, færdiggørelse og understøtter sorteringsprocesser. Systemerne er baseret på højkvalitets kameraer, lyskilder og software, som udfører en analyse af et 2D- eller 3D-billede på en gentagen måde, sammenligner det med de gemte standarder og afvigelsesværdier. Integrationen af visionsystemer med MES-systemer og industrielle automationssystemer understøtter kvalitetsstyringsprocesser i virksomheder. Effekterne af implementeringen af automatiserede kvalitetskontrolsystemer omfatter:
- 24/7 kontinuerlig kontrol af produktkvalitet
- kontrol med 100 % af de fremstillede varer
- øget bevidsthed om processen
- registrering af kontrolresultater i databasen
- eliminering af ventetid i produktionslinjen
- reduktion af antallet af klager
- betydelig stigning i nøjagtigheden af kvalitetskontrol
- reduktion af omkostninger til kvalitetskontrol
Fordele