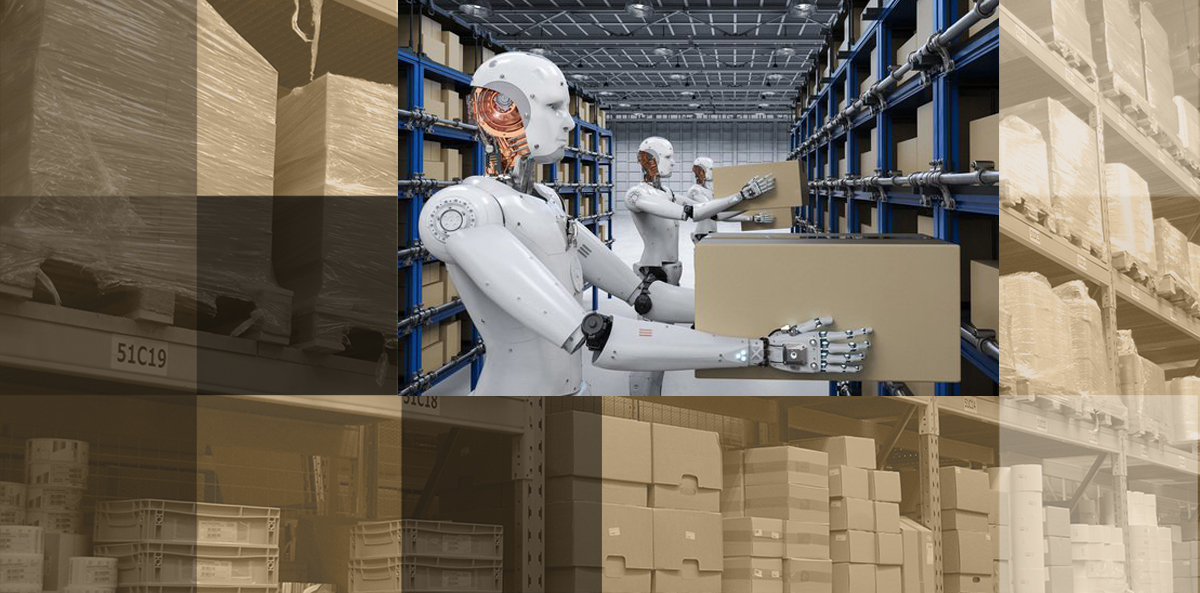
Automated or traditional warehouse – which to choose?
What is the difference between automated and traditional warehouses?
The challenges that industry faces are causing many businesses to consider making far-reaching changes to automation. In recent years warehouse automation in its broadest sense has gained popularity. It is a solution which offers considerable potential savings, optimisation of working hours and many other benefits. However, on the other hand, it raises concerns about implementation costs, complicated management, and the need to reduce staff. What is it really like? What is the difference between an automated warehouse and a traditional one? Which solution will be best for your company? Check it out!
What is warehouse automation?
In a nutshell: automation is about the implementation of modern technologies: machines, algorithms and software which reduce the amount of manual work to a minimum, and most of the tasks related to the warehouse operation happen on their own.
Which areas of warehouse work can be automated? The answer is: all of them. The basic element of an automated warehouse is a maintenance-free device storing basic logistic units on which we accumulate raw materials, products, and goods. In the case of pallets, these will be stacker cranes. Comprehensive automation also provides for integration with the production process. A professionally designed warehouse will therefore be equipped with machines which pick up the prepared components from the production line and transport them to the designated location, e.g., using AGVs. Other machines will then carry out sorting, packaging, and labelling, while others will prepare pallets for shipping. Everything is controlled by specialised software, which must be configured first to meet the needs of a given warehouse.
The benefits of full automation include:
- reduced operating costs;
- reduced lead time;
- increased safety;
- 24/7 capability.
What to pay attention to before deciding on automation:
- costs versus savings from implementation;
- the need for a thorough redesign of the existing warehouse so that it meets the needs of a modern 4.0 industrial hall (if applicable);
- the fixed operating cost of the machine versus the costs of maintaining an employee (for example in seasonal industries).
Which warehouse will be a better choice?
The manual warehouse is a default solution that has so far been used on a much larger scale. In a traditional warehouse, employees are responsible for picking orders, transport, quality control, labelling and shipping of goods. Such a warehouse uses machines; however, these are not autonomous devices, but lifts, pallet trucks etc. operated by employees.
Staying with traditional solutions is not always a bad idea. Smaller companies that do not handle thousands of orders would probably spend more money on implementation of automation than the number of prospective benefits would be.
Manual organisation of work in the warehouse is also a good solution for companies which rely on seasonality to a large extent. They can hire additional employees in the peak season and keep only the necessary staff in the off-season. If the machines were not used for several months a year, their cost would not be recouped as quickly, and they would still need periodic maintenance.
The benefits of the traditional approach include:
- no need to redesign the warehouse;
- less complicated processes;
- easier adaptation to the market demand.
What to pay attention to:
- the human factor entails higher probability of errors, therefore special attention should be paid to quality control;
- need for more frequent recruitment, employee training etc.
Between automated and traditional warehouses
Fortunately for the undecided, it is not necessary to choose “rigidly” between an automated and a manual warehouse. Nothing stands in the way of improving a traditional warehouse by introducing self-operating solutions step by step, for example, investing in automatic lifts which make it easier for workers to cope with heavy loads but do not require drastic changes to the organisation of work in the warehouse or AMRs, self-driving robots, which make it possible to transport goods between designated areas in the warehouse.
The implementation of partial automation may be a prelude to planned large-scale changes, but it may as well end there. Some companies do not need full automation. In their case it will be a challenge to find the golden mean which will make it possible to achieve a noticeably greater efficiency with a simultaneous reduction of the incurred costs.
To be certain that planned automation will have an actual impact on the optimisation of warehouse operation it is worth turning to professionals who deal with the implementation of automatic solutions and conduct pre-implementation analyses. Are you wondering whether an automated warehouse is the right next step in the development of your company? Contact us and we will resolve your doubts and advise you on the best options available.