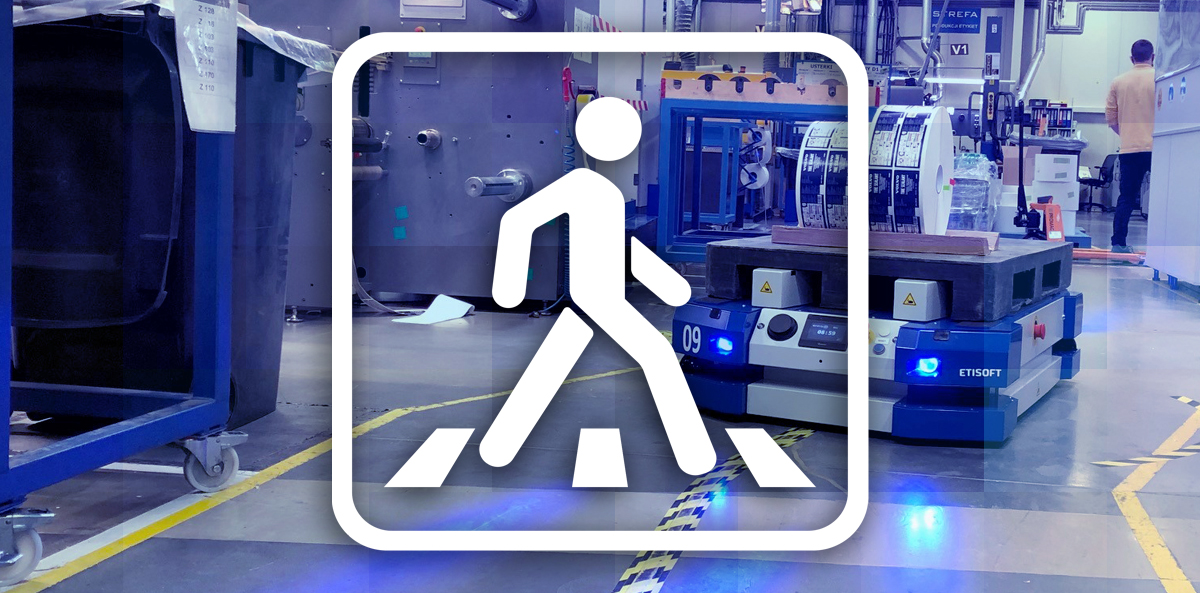
Why won’t a robot run you over? AGV safety systems
When implementing self-driving AGVs, made by experienced Etisoft Smart Solutions engineers, during process automation in production plants, special attention should be paid to the safety aspect.
By choosing our robots, the user can be 100% certain that all the safety requirements have been met at the highest level and in accordance with the guidelines of safety standards, above all with the ISO3691-4 standard -Industrial trucks — Safety requirements and testing — Part 4: Driverless industrial trucks and their systems
Etisoft Smart Solutions approaches each project individually. In the case of adapting the robot’s functionality to a particular customer, a risk analysis is conducted each time. Thanks to that it is easy to identify hazards, provide suitable countermeasures and adapt solutions so that they fully ensure the required level of safety.
The IntraBot series robots are equipped with a range of safety systems which guarantee seamless interaction with people and plant infrastructure. Among them the following ones can be distinguished: a laser space scanner, light and sound signalling, sensors and emergency stop switches.
AGVs and safety measures
Laser space scanners are mounted on robots in a way that makes it possible to fully control the area around the robot. Their task is to prevent collisions with other traffic participants, and they can detect any obstacles encountered. The scanned area is divided into 2 detection zones:
- Protection zone,
- Warning zone.
The protection zone changes depending on the speed, driving direction and status of the robot. The higher the speed of the robot, the longer the protection zone in the driving direction. In the protection zone there are special zones which are active when the robot is moving through a narrow passage, for example. The side zone is then inactive, and the robot moves at a maximum speed of 300 mm/s.
The length of the warning zone is always the same. Detection of an object in the detection zones causes the speed to be reduced or the vehicle to stop completely.
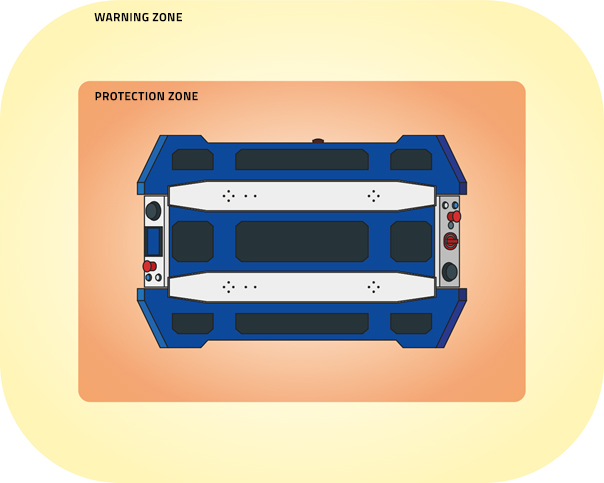
Additionally, the robot is equipped with light and sound signalling
The AGV is coming! It will signal this with light and sound
The IntraBot by Etisoft Smart Solutions has two types of lighting. The first signal is a blue light which casts a glow on the floor in the direction of the robot’s movement. This warns staff about an approaching vehicle. The other type is a backlight which serves an informative function. Depending on the status of the robot, green, yellow, red, white, and blue colours are distinguished.
Additionally, the robot is equipped with a horn and a loudspeaker which perform a warning and informative function.
The horn sound is always used when the robot performs a manoeuvre, for example, drives into loading sections, or retrieves a load. This informs the worker about the need to be particularly careful. There is also a possibility of implementing voice signals, e.g., when the robot detects an obstacle, it “will tell” us about it.
It is also significant to properly mark the whole area where mobile robots operate. This is the final cut in ensuring safety of employees. Any type of load exchange areas, pedestrian walkways and shared pathways should be marked.
In an environment where humans cooperate with autonomous robots, it is extremely important for all workers to be aware of how robots operate and read the external environment. Care must be taken to make sure that workers are thoroughly familiar with basic operation and that they develop the habit of reacting to the various statuses of the robot. Then the robot will become a part of the team.
If you want to have it in your team, please contact us.