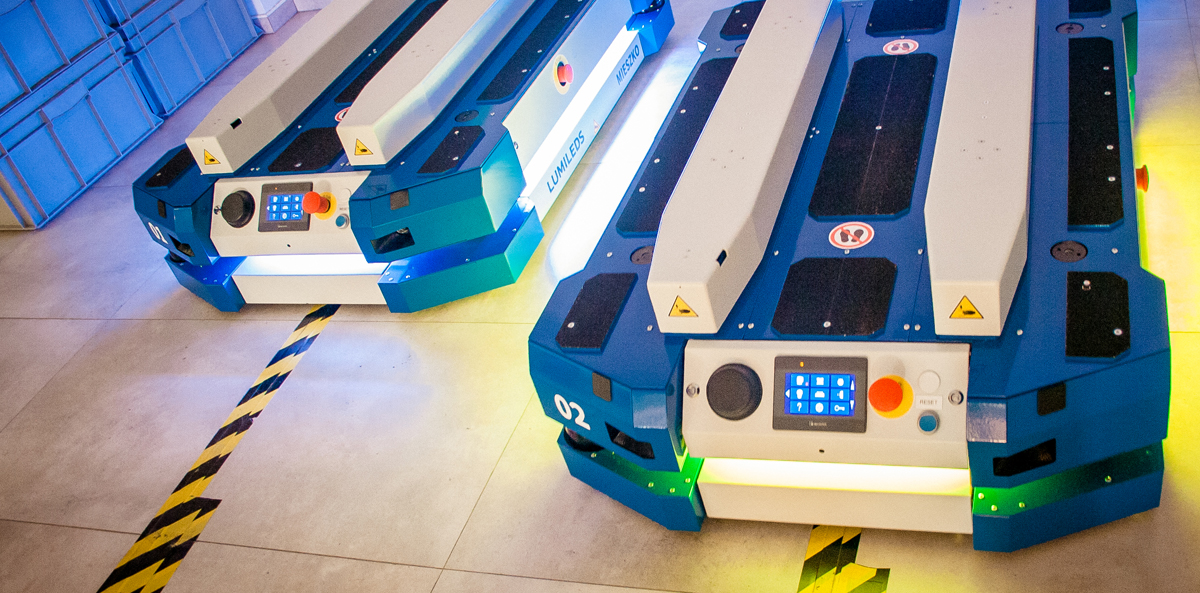
Automation of processes for supplying components to production lines with the use of AMRs/AGVs
In late 2019 and early 2020 Etisoft Smart Solutions carried out a project for a production company, an automotive giant with a global reach. The project was carried out in a Polish plant operating 24/5.
The aim of the project was to automate processes of supplying components to production lines and finished goods to the dispatch area with a capacity of up to 30 pallets per hour while maintaining safety requirements which take into consideration the safety of humans as well as of other vehicles. Planned return on investment in the period shorter than 3 years by, among other things, replacing forklift trucks, reducing labour costs, and guaranteeing performance and continuity of operation during absence of employees, night work and at the weekends.
The scope of the project included:
- Design and simulation of the complete system,
- Delivery, implementation, and integration of a fleet of 6 AMR/AGV Intrabot 550 vehicles with automatic charging stations,
- installation and adaptation of IntraFleet 4.0 software for management of the fleet of AMRs/AGVs (including mission management, robot movement management, reporting, machine book),
- Integration of the ESS Intrafleet with the Customer’s infrastructure,
- Supply of associated infrastructure (buffer roller conveyors, automation, sensors, and IT interfaces),
- an external security audit of the functioning of the system confirming compliance with the standards in force,
- a system operation training and ICT support during and after the implementation of the system,
- final acceptance of the system according to the FAT (Factory Acceptance Tests) specification.
The starting point for the project was the existing organisation of production with several production lines, a manual component picking area and a dispatch area. Internal transport was carried out by 9 employees equipped with hand pallet trucks. On the basis of a 3D scan of the production hall, the requirements and limitations specified by the customer, ESS engineers prepared a draft of the target model of the process. A fleet of 6 AGVs/AMRs and 38 logistics points equipped with associated equipment operated in a 250-metre loop were planned in the system.
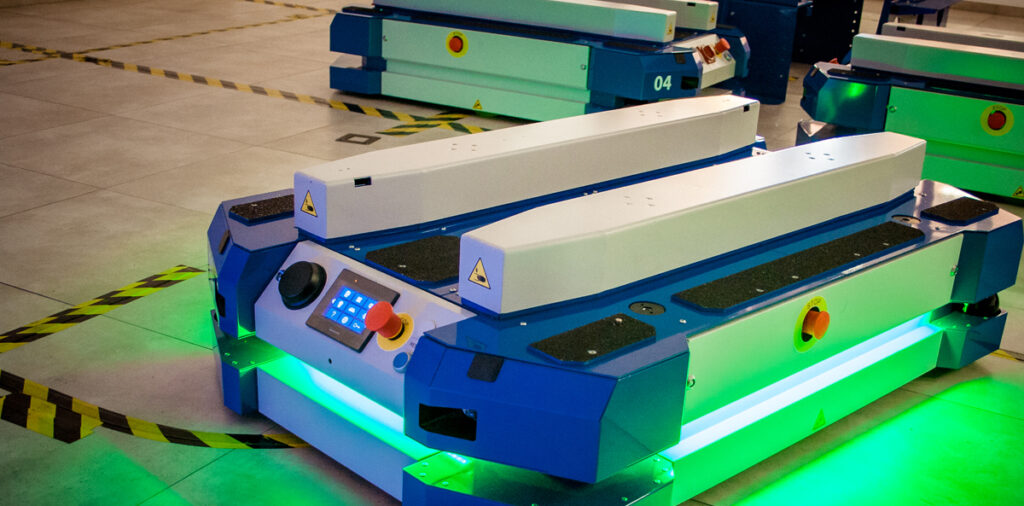
After agreeing the specifications and assumptions of the project with the Customer, an advanced numerical model was made in FlexSim environment taking into consideration external process disturbances. It made the simulation of the designed process in conditions like real ones possible. The analysis conducted in this way confirmed the feasibility of the project according to the adopted assumptions. The results of the numerical simulation indicated that, taking into consideration possible process disruptions and a fleet of 6 AMRs/AGVs operating 24/5, the system can operate at production peaks of up to 30 pallets per hour. The results obtained in this way were verified four months after the project approval during experimental performance tests. The implementation of the system was carried out in production conditions.
Currently, the system operates 24/5 with telephone support, which makes efficient elimination of occasional problems and optimisation of its operation possible. Each month the robots transport several thousand pallets fully operating deliveries to production lines and collecting finished goods and returns.
The intralogistics system, based on AGV/AMR type logistical robots has been recognised in the “Innovative Product for Logistics, Transport and Production 2020” in the 16th edition of the Eurologistic Publishing House competition.
Interested? Contact us!